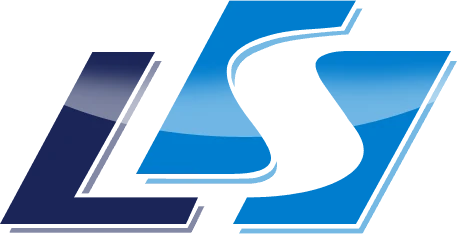
- Lifting Equipment
-
Height Safety
Height Safety Equipment
- Material Handling & Jacking Equipment
- Shop by Brand
- Clearance
-
Contact
Get In Touch
- Home/
- Lifting Equipment/
- General Industrial Lifting Equipment/
- Crane Forks/
- Camlok "TKG-VHS" Self Balance Crane Forks
The TIGRIP TKG-VHS range of crane forks are equipped with adjustable tines, adjustable mast height and a self weight balancing system. Crane forks with self weight balancing* tend to point their tines
upwards when being transported, this prevents the load from unintentionally slipping off the tines.
The self weight balancing mechanism* returns the lifting point to the unloaded position when the load is set down.
- Factor of safety 4 : 1
- Maintenance free.
- Highly visible safety colour.
- For transporting rings or coils, simply push fork tines together.
- Easily adjustable tines for all pallet sizes.
- Supplied with chain for securing the load.
- Never subject the gas spring in automatic forks to heat.
Dimensions & Specifications
Model | WLL (kg) | Adjustment of Tines (A) (mm) | Usable Height (B) (mm) | Length of Tines (C) (mm) | Section of Tines (D) (mm) | Overall Height (E) (mm) | Weight (kg) |
TKG1.0vhs | *200-1000 | 350 - 900 | 1100 - 1600 | 1000 | 100 x 30 | 1420 - 1920 | 140 |
TKG2.0vhs | *400-2000 | 400 - 900 | 1300 - 2000 | 1000 | 120 x 40 | 1655 - 2355 | 220 |
TKG3.0vhs | *600-3000 | 450 - 900 | 1300 - 2000 | 1000 | 120 x 50 | 1720 - 2420 | 280 |
TKG5.0vhs | *1000-5000 | 500 - 1000 | 1300 - 2000 | 1000 | 120 x 60 | 1710 - 2410 | 380 |
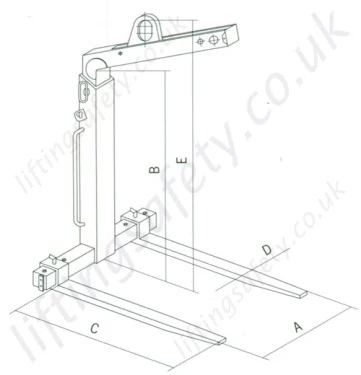
Operation of the Crane Forks
Loading
- Lift the forks off the ground and adjust the tine width if required by turning the plunger and sliding the tine along the box section. Ensure the tine is locked in new position.
- Position the forks centrally alongside the load, just off the ground, with the tines aligned with the tine pockets.
- Slowly move the fork under the load. Minimise swinging of the fork.
- Insert the fork tines to the maximum extent. Never try to pick up a load on the tips of the tines.
Lifting
- Lift and traverse the crane hoist as the trolley moves so that the sling is vertical at all times.Care should be taken when hoisting to ensure the load does not swing back onto you.
- The fork is designed to lean back when loaded. Never continue to lift if the fork leans forward.
- Never stand under a suspended load and when guiding a load by hand always use the handles provided.
- Always stand clear when lifting or lowering.
- Position the hoist above the drop point. DO NOT try to push or pull the load into a position that the normal hoist travel cannot reach.
Unloading
- Lower the load slowly and gently to the ground. Continue to lower until the trolley has returned to the back stop pin moving the crane with the trolley, the trolley is now in the C.O.G of the crane fork.
- Lift the fork just clear of the ground and remove from under the load.
General Safety Instructions
Storage: When not in use always store the crane forks in a floor area clear of danger:
- From collision by fork lift trucks and other machines
- Away from walkways and gangways
- From the effects of wind and rain
Additional Safety
- Never try to lift a load that is longer than the length of the forks.
- Never hold any part of the fork other than the handles provided.
- Never exceed the maximum working load limit.
- Never fast lower always gently lift and lower.
- Never manoeuvre loaded or unloaded forks over personnel.
- Always keep a record of inspections and repairs
- Forks with automatic balance feature require a minimum load of 20% of the W.L.L
- Care should be taken to ensure the load is kept stable when lowering and releasing the crane forks.
- Stand clear when lowering to avoid injury to your feet or legs.
This is by far our best selling range of crane forks. They are manufactured by Camlok who are a trade manufacturer and part of the CMCO group of lifting equipment companies.
The TIGRIP TKG-VHS range of crane forks are equipped with adjustable tines, adjustable mast height and a self weight balancing system. Crane forks with self weight balancing* tend to point their tines
upwards when being transported, this prevents the load from unintentionally slipping off the tines.
The self weight balancing mechanism* returns the lifting point to the unloaded position when the load is set down.
- Factor of safety 4 : 1
- Maintenance free.
- Highly visible safety colour.
- For transporting rings or coils, simply push fork tines together.
- Easily adjustable tines for all pallet sizes.
- Supplied with chain for securing the load.
- Never subject the gas spring in automatic forks to heat.
Dimensions & Specifications
Model | WLL (kg) | Adjustment of Tines (A) (mm) | Usable Height (B) (mm) | Length of Tines (C) (mm) | Section of Tines (D) (mm) | Overall Height (E) (mm) | Weight (kg) |
TKG1.0vhs | *200-1000 | 350 - 900 | 1100 - 1600 | 1000 | 100 x 30 | 1420 - 1920 | 140 |
TKG2.0vhs | *400-2000 | 400 - 900 | 1300 - 2000 | 1000 | 120 x 40 | 1655 - 2355 | 220 |
TKG3.0vhs | *600-3000 | 450 - 900 | 1300 - 2000 | 1000 | 120 x 50 | 1720 - 2420 | 280 |
TKG5.0vhs | *1000-5000 | 500 - 1000 | 1300 - 2000 | 1000 | 120 x 60 | 1710 - 2410 | 380 |
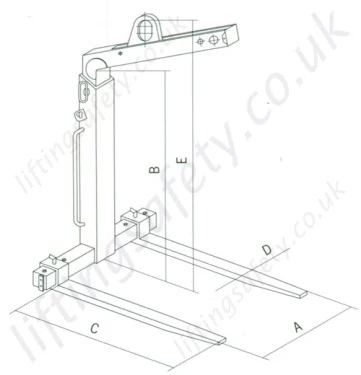
Operation of the Crane Forks
Loading
- Lift the forks off the ground and adjust the tine width if required by turning the plunger and sliding the tine along the box section. Ensure the tine is locked in new position.
- Position the forks centrally alongside the load, just off the ground, with the tines aligned with the tine pockets.
- Slowly move the fork under the load. Minimise swinging of the fork.
- Insert the fork tines to the maximum extent. Never try to pick up a load on the tips of the tines.
Lifting
- Lift and traverse the crane hoist as the trolley moves so that the sling is vertical at all times.Care should be taken when hoisting to ensure the load does not swing back onto you.
- The fork is designed to lean back when loaded. Never continue to lift if the fork leans forward.
- Never stand under a suspended load and when guiding a load by hand always use the handles provided.
- Always stand clear when lifting or lowering.
- Position the hoist above the drop point. DO NOT try to push or pull the load into a position that the normal hoist travel cannot reach.
Unloading
- Lower the load slowly and gently to the ground. Continue to lower until the trolley has returned to the back stop pin moving the crane with the trolley, the trolley is now in the C.O.G of the crane fork.
- Lift the fork just clear of the ground and remove from under the load.
General Safety Instructions
Storage: When not in use always store the crane forks in a floor area clear of danger:
- From collision by fork lift trucks and other machines
- Away from walkways and gangways
- From the effects of wind and rain
Additional Safety
- Never try to lift a load that is longer than the length of the forks.
- Never hold any part of the fork other than the handles provided.
- Never exceed the maximum working load limit.
- Never fast lower always gently lift and lower.
- Never manoeuvre loaded or unloaded forks over personnel.
- Always keep a record of inspections and repairs
- Forks with automatic balance feature require a minimum load of 20% of the W.L.L
- Care should be taken to ensure the load is kept stable when lowering and releasing the crane forks.
- Stand clear when lowering to avoid injury to your feet or legs.
This is by far our best selling range of crane forks. They are manufactured by Camlok who are a trade manufacturer and part of the CMCO group of lifting equipment companies.
You May Also Like
Contact Us About This Product
If you wish to receive a quote for this product, please use the tab above, this form is for general enquiries regarding this product only.
You can also Request a Quote using the Quote tab above!
You can easily add more than one item to the Quote Request. This is highly recommended as we will be able to suit your needs much more efficiently.