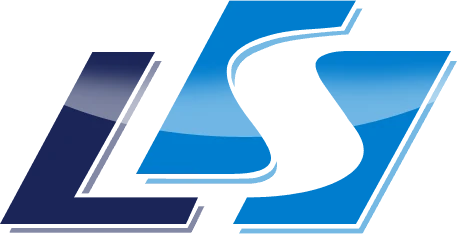
The Verification of Spreader Beams, Lifting Beams and Lifting Frames.
Document reference LEEA 055 version 2 dated 6th March 2019
Disclaimer
The content of this guidance is provided for general information only. Whilst it is intended to represent a standard of good practice, it has no legal status and compliance with it does not exempt you from compliance with any legal requirements. If you require advice on your specific circumstances, please contact one of our advisors.
Although we make reasonable efforts to update the information in our guidance, we make no representations, warranties or guarantees, whether express or implied, that the content of our guidance is accurate, complete or up-to-date. It is the responsibility of those with specific duties under the legislation to ensure that they fulfil the obligations imposed on them
1.0 Introduction.
Spreaders beams, lifting beams and lifting frames are used for a wide range of lifting operations throughout most industrial sectors. They are classified as lifting accessories under the Supply of Machinery (Safety) Regulations 2008 and the Lifting Operations and Lifting Equipment Regulations 1998. These accessories are often bespoke in design and commonly produced as ‘one offs’ or in small batches. They can also be designed so that they can be adjusted to suit different loads. This adjustment is sometimes achieved by a modular design of sections that can be bolted together in a range of configurations, or by means of multiple or adjustable attachment points. However, it should be noted that designers can use a variety of other techniques to provide the adjustment.
As the name suggests, spreader beams were originally a simple strut used to spread apart a two leg sling to prevent damage to the product being lifted from the compressive forces induced by the sling. Now the term is used for any beam suspended from its ends by a sling so that the beam is loaded in compression, see figure
Figure 1 - Spreader Beam
The term lifting beam is used for a beam suspended from a more central point so that the beam is loaded in bending, see figure 2.
Figure 2 - Lifting Beam
Lifting frames comprise of multiple structural members, sometimes combining members in compression and bending, see figure 3.
Figure 3 - Lifting Frames (4-point lifting or spreader beams)
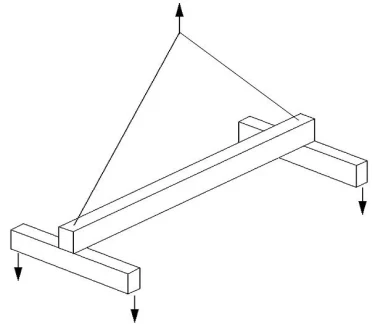
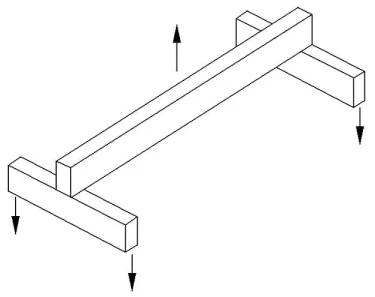
For the purposes of this guide, spreader beams, lifting beams and lifting frames are referred to under the generic name of lifting beams.
Lifting beams are often used in combination with slings and other accessories such as vacuum lifters, lifting magnets and plate clamps to provide the connection to the load.
2.0 Standards and Legislation.
Lifting beams are classified as lifting accessories and fall within the scope of The Supply of Machinery (Safety) Regulations 2008. The harmonized standard for new lifting beams is BS EN 13155: 2003+A2: 2009 Cranes – Safety – Non-fixed load lifting attachments. This standard should be adopted as best practice to ensure conformity to the minimum requirements of the Machinery Directive.
Note: This standard is currently under revision. If any changes are made which affect lifting beams, this guidance will be revised accordingly.
Prior to this standard and the Directive there was no specific standard for the manufacture of lifting beams. Manufacturers would often, therefore, work to the requirements of other standards for welded structural steels, such as BS 449 and BS 2573. For the testing of lifting beams, the requirements contained in the International Labour Organisation (ILO) code of practice ‘Safety and health in ports’ was also commonly used.
Once in service lifting beams fall under the Provision of Use of Work Equipment Regulations (PUWER) and the Lifting Operations and Lifting Equipment Regulations (LOLER).
3.0 Design, Manufacture and Verification of Lifting Beams.
It is important that lifting beams fully comply with The Supply of Machinery (Safety) Regulations 2008. That includes lifting beams manufactured by the user. This part of the guidance addresses the criteria that must be considered.
3.1 Technical File.
The technical file is very important and must contain all the information relevant to the manufacture of the lifting beam. Should a lifting beam fail in service, then it is this technical file that will be scrutinised. If it cannot be proven that other factors, such as misuse, were the cause of the failure, then the manufacturer will rely upon the technical file to show that everything reasonably practicable was done to ensure the safety of the equipment.
The technical file does not have to be a physical entity, but it must be possible to assemble it from various sources should the need arise. Typical information that should form a technical file for lifting beam is as follows:
- A list of the Essential Health and Safety Requirements (EHSRs) which apply to the lifting beam.
- A description of the methods used to eliminate hazards or reduce risks.
- A list of standards to which the equipment has been made. This should include standards used for accessories that are supplied fitted to the beam, such as shackles, chains, wire ropes, etc.
- Information from the user. This should include such detail as to the geometry and mass of the load and position of the centre of gravity. Details of the lifting appliance should be included, such as the size of the hook and the WLL. The work envelope between the appliance and the load is also important.
- Design information. Calculations, detailed drawings, fabrication / welding procedures.
- Material traceability. Details of all materials and assemblies should be retained in the technical file. This could be a mill certificate for steelwork or an EC Declaration of Conformity for a sling.
- Test reports. These could be the reports of a load test or a non-destructive test done on the welds.
- Instructions for use.
The technical file is the evidence which supports the EC Declaration of Conformity for the lifting beam. The EC Declaration of Conformity should be added to the technical file and a copy should accompany the lifting beam.
3.2 Verification methods
With regard to strength, there are two main criteria to verify:
- At the proof force, the maximum stress must be within the yield stress of the material being used.
- At the minimum failure force, the load must not be released.
It is acceptable to verify these criteria using either of, or a combination of, two techniques, calculation or load test. Sections 3.2.1 and 3.2.2 address each method.
In some cases the lifting beam will be designed such that it can rotate or tilt. It may also have moving parts that can move along the beam. These items require additional design and verification. Section 3.2.3 addresses lifting beams with moving parts.
It is important to note that lifting beams must be able to tolerate an angle of up to 6 degrees above their normal plane of lifting. Therefore, this must be considered when using any of the verification methods in 3.2.1, 3.2.2 and 3.2.3.
3.2.1 Verification through Calculation.
The person producing the calculations must be competent for the purpose, have sufficient theoretical knowledge and experience of lifting beams to ensure that the design is safe and fit for purpose. It is also recommended that there is a procedure in place to ensure that these calculations are suitably checked. However, it should be noted that this does not necessarily have to be done by another competent person, as often or not computer simulation is used in the verification of lifting beams. When using computer simulation for the design it is advisable that the results are checked by simple hand calculation. In this case the person checking the computer simulation must be competent for the purpose. The hand calculations used should be sufficient to ascertain if the stress is about right or if the beam is deflecting the correct way.
The calculations used and / or computer simulation must accurately simulate the in-service forces that will be induced by the load. Consideration must be given to the nature of the load. For example, is it flexible or rigid? If the load is flexible, then the beam may require sufficient rigidity to prevent the load being damaged. Conversely a rigid load may require some flexibility in the lifting beam to ensure uniformity of loading.
Examples of the type of calculation that must be considered are as follows:
- Critical buckling loads.
Note: In some spreader beams the compression load will be applied eccentrically due to the shackle point being offset from the beam axis by the pad eye. Solving equations for eccentric buckling can be quite time consuming as the critical buckling load cannot be solved explicitly and a root-finding technique using numerical methods has to be used. To save time designers often use widely accepted computational methods where successive substitution with assured convergence can be applied. MathCAD and FEA are examples of such software.
- Bending, shear and torsion stresses.
- Lateral buckling of the flange or web of a beam. (Refer to BS EN 1993-1-1 clause 6.3 for guidance)
- Shear and bearing stresses for pad eyes.
- Weld or bolt stress calculations (note a minimum of grade 8.8 bolts should be used).
- Brittle fracture. Refer to table A.3 of BS EN 13155.
The limiting factors imposed by EN 13155 are that at two times WLL the maximum stress must be within the yield stress of the material being used. At three times the WLL a nonlinear analysis of the structure must be done to ensure that critical parts of the structure will not fail such that the load is released, although permanent deformation is allowed.
Note: The design factors only take into consideration the dynamic effects of lifting and do not include wind loads. Depending on the environment where the lifting beam is to be operated the wind pressure load on the item being lifted and the structure itself may also need to be included in the analysis.
The position of the lifting points on the load will affect stability if they are at or below the Centre of Gravity (COG).
It should be noted that the design calculations, being based on idealistic theoretical assumptions, cannot account for everything. It is therefore recommended that the beam is inspected at critical stages of the manufacturing process to check the quality of load bearing assemblies, weld preparations and welds. The extent of these inspections is at the discretion of the designer and may include NDT of critical welds.
3.2.2 Verification through test.
A load test should always be planned on the assumption that the item under test might fail. Adequate precautions should be in place to prevent injury to any persons or damage to anything other than the item under test.
If the minimum failure force is not verified by calculation, then, when using this method alone, at least one lifting beam will have to be destroyed.
An adequate test specification must be drawn up against the design criteria. Acceptance criteria, such as maximum permissible deflections or deformations for worst case loading conditions, must be included in the specification.
For modular or adjustable lifting beams the worst case configuration(s) must be used for the test.
To meet the design criteria the test must accurately simulate the in-service loading conditions for which the beam has been designed, including a tolerance on orientation in use.
There are two common types of load testing that can be deployed by the tester to achieve this and they are described as follows:
1. Load testing with weights.
- Test weights must be pre-weighed or used with a load cell in the line.
- The lifting appliance must be of adequate strength with sufficient head room.
- For higher capacity beams, containers may be required to house the weights and the self-weight of these containers must be considered.
- For loads that can flex, the test weights must be applied such that they can accurately simulate this affect. To achieve this may require a jig or mock-up of the load to be fabricated. This may even require a controlled lift of the product to be lifted. However, testing by means of applied force may prove more accurate and cost effective in this instance.
- For loads that are rigid, the test weights must act as a single rigid load.
2. Load testing by means of an applied force.
- - The force can be applied by means of hydraulic or pneumatic actuators or by mechanical means such as wire rope pulling machines.
- - The test rig(s) must have a calibrated load sensor or a calibrated load cell must be used in the load path. This equipment must be calibrated to BS EN 7500-1 and have an accuracy of not less than ±2%
- - By fixing the beam at the point where the lifting appliance hook would fit, it is possible to use multiple applied force devices, with variable loads and amplitudes to accurately simulate a flexible load.
- - Using this method it is possible to undertake separate tests for various elements of the lifting beam.
To ascertain whether or not the acceptance criteria has been met, the tester will need to use measuring equipment. This measuring equipment will depend on the acceptance criteria, but it must be calibrated, and may include dial test indicators, strain gauges, etc. Equipment used for measuring deflections must have a resolution such as to allow the measurement to within ±5% of the permitted deflection of the structure under test.
Following the proof force test the beam must be thoroughly examined. This examination may include an NDT of the critical welds.
Other details of the thorough examination can be found in section 4.0 of this guidance.
3.2.3 Verification of lifting beams with moving parts.
If the lifting beam is designed to tilt, then the manufacturer is responsible for specifying the maximum permissible tilt from the horizontal. The beam can be verified through calculation or test, but whichever method is used, it is important that all the criteria specified in 3.2.1 and 3.2.2 are addressed with the beam at an additional 6 degrees to the maximum intended tilt angle.
Some lifting beams may be required to tilt under load in order to manipulate or orientate the load. In this case the test should be repeated at several positions throughout the range of movement. These positions should be selected to simulate the worst operational conditions and take account of the tilting tolerance required.
Some lifting beams may have a tilting or rotating mechanism. If the free movement of the tilting or rotating mechanism presents a hazard then it is important that the mechanism is equipped with a device to stop movement and to immobilise the load in its intended position.
In addition to the above some lifting beams will also have movable parts, such as pad eyes that can be adjusted along the length of the beam. It is important that any movable part is effectively held in place when under load. When the spacing between these moving parts is controlled by a power source, protection devices must be incorporated to prevent crushing and shearing hazards as specified in BS EN 349:1993+A1:2008.
The devices described above, to hold the movable component of the lifting beam in place under load, must be effective up to 6 degrees above the maximum intended tilting angle. If the devices use friction then the frictional force should be at least twice the force due to the self-weight of the parts and the working load limit at the maximum intended tilting angle plus 6 degrees.
As with the main structural calculations the verification of the restraining device can be done by calculation or by test. Each method is detailed as follows:
- 1. Calculation – The calculations should address all the criteria as outlined in section 3.2.1. However, if the beam can tilt then the analysis should be undertaken with the beam at plus 6 degrees from the maximum intended tilting angle. If the devices use friction, the calculations shall demonstrate that the frictional force is at least two times the force due to the self-weight of the parts and the working load limit at the maximum intended tilting angle plus 6 degrees.
- 2. Test – The criteria set out in 3.2.2 should be followed in addition to the following procedure.
With the moving part locked in position by means of its locking mechanism, a force equal to two times the WLL should be applied for a minimum of 1 minute at an angle of 6 degrees in excess of the maximum intended angle. The test should be carried out in both directions about the horizontal axis for each available locking position. If the moving part does not have a predetermined position but locks by friction, the test must be carried out at the two extremes of travel and at one intermediate part.
After the force has been removed, the moving part and the locking mechanism must be thoroughly examined by a competent person.
To be considered acceptable, the part and the locking mechanism must sustain the load without slippage, deformation or failure. After release of the load there must not be any visible defects and the device must still operate freely.
3.2.4 Verification of ancillary items.
Most lifting beams will be fitted with supplementary lifting accessories that are used to connect the lifting beam to the load and / or the lifting appliance. Examples of such accessories are typically, slings, grabs, clamps, magnets and vacuum lifters.
For ancillary equipment that has been bought in, information such as the EC Declaration of Conformity, manufacturer’s certificate and instructions for use and maintenance must be included in the technical file for the beam assembly. The instructions for use must be supplied with the beam assembly or incorporated in the beam assembly’s instructions for use and maintenance.
Other items should be verified in accordance with an appropriate harmonised standard. Common standards to consider would be BS EN 13155, BS EN 818 series and BS EN 13414 series.
3.3 Attaching the lifting beam to the crane and load.
Connections to the crane or the load should be capable of being locked before lifting so as to prevent any accidental uncoupling. For example a shackle with a bolt, nut and cotter pin should be used.
If the lifting beam has suspended parts, means shall be provided to protect them from damage during coupling or uncoupling of the lifting beam and crane.
If the lifting beam has moving parts that can be moved along the beam, there should be a means at each end of the beam to prevent them from falling off. These moving parts must also have a device that will lock them in position when under load. If the means of locking the load attachment points is operated manually, then the state of locking must be visible to the operator.
3.4 Storage.
It is important that when the lifting beam is not required for use it can be set down and stored such that it stable and protected from damage.
To be regarded as stable it must not tip over when tilted to angle of 10 degrees in any direction. This can be achieved by adding feet or by the provision of additional equipment such as a stand.
If the lifting beam is fitted with ancillary items then the storage should also provide effective protection for them. Alternatively these items should be removed and stored separately. In the latter case the identity of the equipment must be maintained.
3.5 Instructions for use and maintenance.
Instructions for use and maintenance must be supplied with the beam. The LEEA has produced numerous safety information leaflets that can be used as a guide to the production of such a document, most notably reference to SI 8.3 Lifting Beams and Spreaders should be made.
For modular lifting beams details of the range of configurations and associated safe working loads should also be included. This can be done by means of detailed assembly drawings.
If the orientation of the beam is not obvious, this information should be provided and schematics are the simplest method of doing this.
3.6 Documentation
Lifting beams are classified as lifting accessories and are within the scope of The Supply of Machinery (Safety) Regulations 2008. Therefore they must be supplied with an EC Declaration of Conformity and instructions for use and maintenance.
The EC Declaration of Conformity must contain the following information:
- The name and address of the manufacturer.
- The name and address of the manufacturers authorised representative.
- The name and address of the person responsible for compiling the technical file.
- Description of the equipment, type, serial number and WLL.
- The standards and specifications used.
- The place and date of the declaration.
- A declaration claiming conformance with the essential health and safety requirements as defined in the directive 2006/42/EC
- Name, position and signature of the person making the declaration.
3.7 Marking
The lifting beam must be marked with the following information:
- The name and address of the manufacturer.
- The CE mark
- The serial number.
- Year of construction.
- Total mass of the assembly.
- Maximum working load in tonnes or kilograms.
Note 1: Some lifting beams have multiple lifting points and the maximum working load may depend upon the lifting points in use. The marking must clearly show the permitted options and the maximum working load for each.
Note 2: Some lifting beams are of modular design and the maximum working load may depend upon the configuration. If it is impractical to show the maximum working load for all configurations, a code may be used to identify the capacity of each component part and that code used in the manufacturer’s instructions to determine the maximum working load for the particular configuration.
Note 3: Where the orientation of the beam is not obvious, this should also be indicated. A ‘this way up’ arrow may suffice.
Note 4: Occasionally lifting beams are fitted with fork lift pockets. These pockets are either intended to allow a fork lift truck to lift the load with the lifting beam or to allow the beam to be moved from location to location only. Whatever the intention, it is important that they are marked appropriately.
4.0 In-service Lifting Beams
Under LOLER lifting beams are considered as lifting accessories and must be examined at least every 6 months or in accordance with and examination scheme (refer to LEEA 032 for guidance) and after exceptional circumstances. The examinations should include the following:
- Check for clear identification number.
- Check for clear marking of WLL.
- Check for clear marking of the self-weight.
- Check main body of beam is free from distortion, corrosion, cracks, gouges, or wear.
- Check all welded connections are free from cracking or corrosion.
- Check that any bolted connections are free from corrosion and cracking and that all are secure using the correct bolts.
- Check that any shackles are free from distortion, nicks, gouges or wear.
- Check that all shackle pins are captivated preferably with a nut and pin arrangement.
Note: This list is not exhaustive and some configurations may require additional checks.
From time to time lifting equipment companies will be asked by owners of lifting beams to overload test their lifting beam. This is due to a lack of knowledge of current legislation and it is the Lifting Equipment Engineers Association’s advice that lifting equipment companies take a position of responsibility and advise end users of the requirements.
The general advice is that the traditional routine overload testing of lifting equipment has a number of disadvantages as follows:
- Some manufacturers do not recommend overload tests, except in exceptional circumstances, and severely limit the magnitude of the test load that may be applied.
- Repeated overloads can cause deterioration of the lifting beam’s structure over time.
- Most structural failures are the result of fatigue and such defects will not be revealed by an overload test. Fatigue cracking can be identified during the thorough examination.
- There is no defined structural or mechanical benefit.
- A significant number of insurance policies do not provide cover for lifting equipment that has been overloaded in any circumstances, including overload testing.
In summary, where a defined scope of examination approach is used, overload testing is not required unless deemed necessary by the competent person.
The request to test might arise because the lifting beam has been modified or manufactured new by the user. The user may expect the lifting equipment company to ‘certify’ the lifting beam as safe to use. However in this case, whilst the lifting equipment company can advise, the user is legally responsible and should specify the tests required. Generally it should be tested in accordance with EN 13155 if new, or in accordance with the standard to which it was originally designed if not. The lifting equipment company should carry out the tests specified and issue a report of test stating what was done and the results. The report should clearly state that it is a report of test only and that to put the equipment into service an EC Declaration of Conformity (for a new lifting beam) or a LOLER report of thorough examination (if the modification is not so substantial that it is considered to be a new lifting beam) is required.
4.1 Verification of repaired lifting beams.
Lifting beams will inevitably get knocked about or even misused in service resulting in damage and the need for repair. Whenever a lifting beam requires repair it is advisable that the cause of the damage be investigated. It may be that the equipment is no longer adequate for the task.
4.1.1 Repair and verification due to in-service wear and tear.
If a beam is to be repaired it is advisable that the original design specification is consulted. Where this is not feasible then the repairer will have to take responsibility to ensure that the correct materials and components are used. To that end the repairer must have adequate information about the application the lifting beam is used for.
A record of the repairs and details of the components used should be recorded and retained with the maintenance log of the equipment.
Following the repair the equipment should be thoroughly examined by a competent person. If the repair might affect the load bearing capability, the thorough examination may include NDT and / or a load test.
4.1.2 Modification and verification.
There are a variety of reasons why a lifting beam will be modified during its life. It may be that the product it lifts has been altered requiring different distances between lift points or an increase in weight for example.
Whatever the reason it is important that the original design specification, test data, and technical file is referred to where possible. In the absence of this information then the person responsible for the modification will have to make assumptions about certain aspects of the design in order to minimise the risk. For example, assume the lowest grade of steel for calculation purposes.
The modification should then be treated as making a new lifting beam from second hand materials and sections 3.0 – 3.7 of this guidance will apply.