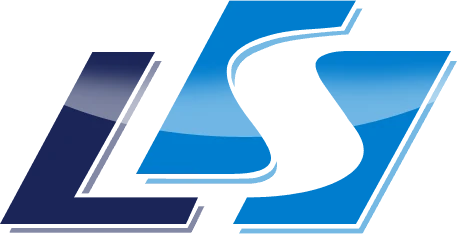
- Lifting Equipment
-
Height Safety
Height Safety Equipment
- Material Handling & Jacking Equipment
- Shop by Brand
- Clearance
-
Contact
Get In Touchsales@liftingsafety.co.uk +44 (0)1977 684 600
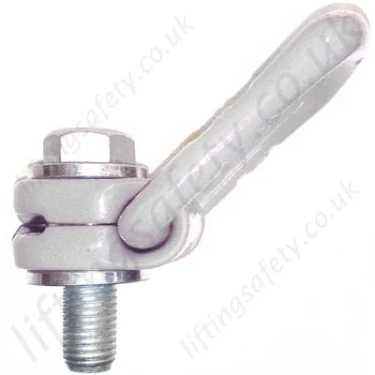
Rud "LBG" Stainless Swivel Hoist Rings, Rotating Swivel Lifting Eye Bolt. Metric Thread - Range from 1000kg or 2000kg
RUD LBG Stainless Steel Bolt-on Swivel Load Rings.
LBG INOX / SBS-3137
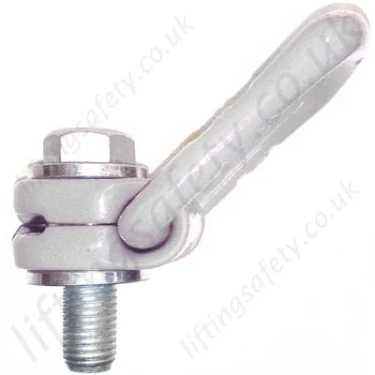
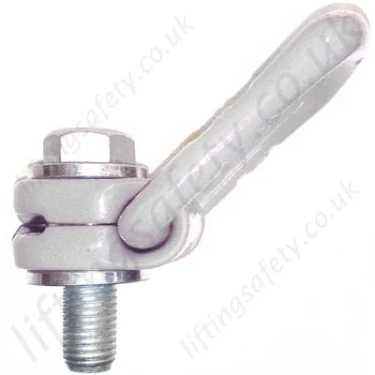
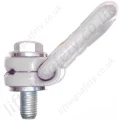
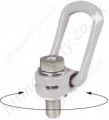
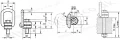
Unfortunately the RUD LBG Stainless Hoist ring is no longer available. Please see our range of stainless steel lifting points for a possible alternative.
Can rotate through 360 degree, automatically adjusting to the adjusted to the direction of the lift.
The RUD lifting ring LBG swivel hoisting rings can rotate by 360°, aligned to the direction of lift, the load ring can be tilted and will give 100% WLL in all load directions. The bolt supplied with the LBG is captivated so that it becomes a part of the lifting assembly and is 100% crack detected. The maximum lengths of the screws are adjusted in a way that a material thickness of about 8xM (with M16 and M20) and can be mounted by using a hexagon nut (ISO 7084/7090).
Lifting safety can supply special length bolts to our customers specification.
For technical information please see the Load Charts, Technical Specifications or User Instructions tabs above.
Proof Testing
There is no requirement to Proof Test RUD Products, either Bolt or Weldable after Installation if the user instructions for welding are carried out correctly. The welding should be carried out by a suitably qualified and competent welder/person.
The supporting structure, or the load, should be of adequate strength to take the stresses involved and this is the responsibility of the engineering designer or equivalent.
RUD Lifting and Lashing Products are Manufactured and conform to EN 1677. No further Proof Testing in the field is required. In fact it would be considered that the Product had been overloaded if a Load more than the recommended Working Load Limit had been applied.
RUD products should be regularly inspected in line with the requirements of LOLER and as per our user instructions at intervals decided by a competent person.
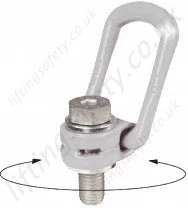
Load Charts - Metric and Imperial
Load Capacities - Metric Tonnes - Table 1
Method of lift | ![]() |
![]() |
![]() |
![]() |
![]() |
![]() |
![]() |
![]() |
|||
Number of legs | 1 | 1 | 2 | 2 | 2 | 2 | 2 | 3 and 4 | 3 and 4 | 3 and 4 | |
Angle of inclination <ß | 0° | 90° | 0° | 90° | 0-45° | 45-60° | unsymm. | 0-45° | 45-60° | unsymm. | |
Factor | 1 | 1 | 2 | 2 | 1,4 | 1 | 1 | 2,1 | 1,5 | 1 | |
Type Thread | WLL in metric tonnes, bolted and adjusted to the direction of pull | ||||||||||
LBG 1t | M16 | 1 t | 1 t | 2 t | 2 t | 1.4 t | 1 t | 1 t | 2.1 t | 1.5 t | 1 t |
LBG 2t | M20 | 2 t | 2 t | 4 t | 4 t | 2.8 t | 2 t | 2 t | 4.2 t | 3 t | 2 t |
Load Capacities - Imperial lbs - Table 2
Method of lift | ![]() |
![]() |
![]() |
![]() |
![]() |
![]() |
![]() |
![]() |
|||
Number of legs | 1 | 1 | 2 | 2 | 2 | 2 | 2 | 3 and 4 | 3 and 4 | 3 and 4 | |
Angle of inclination <ß | 0° | 90° | 0° | 90° | 0-45° | 45-60° | unsymm. | 0-45° | 45-60° | unsymm. | |
Factor | 1 | 1 | 2 | 2 | 1,4 | 1 | 1 | 2,1 | 1,5 | 1 | |
Type Thread | WLL in imperial lbs, bolted and adjusted to the direction of pull | ||||||||||
LBG 1t | M16 | 2200 lbs | 2200 lbs | 4400 lbs | 4400 lbs | 3086 lbs | 2200 lbs | 2200 lbs | 4630 lbs | 3307 lbs | 2200 lbs |
LBG 2t | M20 | 4400 lbs | 4400 lbs | 8800 lbs | 8800 lbs | 6172 lbs | 4400 lbs | 4400 lbs | 9260 lbs | 6614 lbs | 4400 lbs |
Technical Dimensions - Table 3
All dimensions are in millimetres (mm) unless otherwise stated.
|
|||||||||||||||||||||||||
Model | WLL (t) | Weight (kg) | A (mm) | B max. | C | D | E | F | G | H std. | H max. | J | K | L std. | L max. | M (mm) | N | SW | R | T | DB | Thread Pitch (mm) | torque | Standard | |
Metric Threads | |||||||||||||||||||||||||
LBG (3) M16 RS 1t | 1 | 1 | 50 | 85 | 50 | 45 | 43 | 16,5 | 38 | 25 | - | 95 | 45 | 63 | - | 16 | - | 24 | 46 | 88 | 40 | 2 | 100 Nm | 62086 INOX | |
LBG (3) M20 RS 2t | 2 | 1,1 | 50 | 85 | 50 | 46 | 42 | 16,5 | 38 | 27 | - | 95 | 45 | 65 | - | 20 | - | 30 | 46 | 88 | 40 | 2.5 | 200 Nm | 62813 INOX |
User Instructions
1. Reference should be made to German Standards accord. BGR 500 or other country specific statutory regulations and inspections are to be carried out by competent persons only.
2. Before installing and every use, visually inspect RUD lifting points, paying particular attention to any evidence of corrosion, wear and weld cracks and deformations. Please ensure compatibility of bolt thread and tapped hole.
3. The material construction to which the lifting point will be attached should be of adequate strength to withstand forces during lifting without deformation. The German testing authority BG, recommends the following minimum for bolt lengths:
1 x M in steel (minimum quality S235JR [1.0037])
1,25 x M in cast iron (for example GG 25)
2 x M in aluminium alloys
2,5 x M in aluminium-magnesium alloys
( M = diameter of RUD lifting point bolt, for ex. M 20 )
When lifting light metals, nonferrous heavy metals and gray cast iron the thread has to be chosen in such a way that the working load limit of the thread corresponds to the requirements of the respective base material.
RUD lifting points are delivered with a 100 % crack tested bolt (length up to lmax please see chart 2). When using your own bolts, the bolts have to be 100% crack tested. The min quality of the hexagon bolt had to be 10.9 accord. EN 24014 (DIN 931) with the nominal diameter. For replacement the bolt can be easily hammered out (M8 - M30). The type VLBG 7t M36 is only delivered with a special bolt, therefore it is not possible to use a EN/DIN-bolt.
RUD supplies the Vario length complete with a washer and crack-detected nut corresponding to DIN 980.
4. The lifting points must be positioned on the load in such a way that movement is avoided during lifting.
a.) For single leg lifts, the lifting point should be vertically above the centre of gravity of the load.
b.) For two leg lifts, the lifting points must be equidistant to/or above the centre of gravity of the load.
c.) For three and four leg lifts, the lifting points should be arranged symmetrically around the centre of gravity in the same plane if possible.
5. Load Symmetry:
The working load limit of individual RUD lifting points are calculated using the following formula and are based on symmetrical loading:
WLL =
|
G n x cos ß |
WLL = Working Load Limit G = Load Weight (kg) n = Number of load bearing legs ß = Angle of inclination of the chain to the vertical |
The calculation of load bearing legs is as follows:
No. Legs | Symmectrical | Asymmetrical |
Two Leg | 2 | 1 |
Three / Four Leg | 3 | 2 |
(See Table 1 and 2)
6. A Plane bolting surface (ØDB) must be guaranteed. The holes must be drilled with a sufficient depth in order to guarantee compatibility with the supporting surface.
7. The LBG has to be adjustable through 360° when fitted.
For single use just tighten with spanner. For long term application the VLBG should be tightened with torque according to table 2 (+/- 10%).
In case of turning movements (continuous operation) the recommended torques have to be checked regularly (For turning movements we recommend to use the RUD lifting point PowerPoint, WBG-V or WBG).
Adjust to the direction of pull, before attaching to the lifting means. The load ring should be free moving and should not be touching edges.
8. All fittings connected to the VLBG should be free moving. When connecting and disconnecting the lifting means (sling chain) pinches and impacts should be avoided. Damage of the lifting means caused by sharp edges should be avoided as well.
9. To prevent unintended dismounting through shock loading, rotation or vibration thread locking fluid such as Loctite (depending on the application, please pay attention to the manufacturer's instruction) could be used to secure the bolt, or use form-closed devices.
10. Effects of temperature:
Due to the DIN/EN bolts that are used with the VLBG the working load limit should be reduced accordingly:
-40° to 100°C = no reduction (-40°F to 212°F)
100° to 200°C = minus 15% (212°F to 392°F)
200° to 250°C = minus 20% (392°F to 482°F)
250° to 350°C = minus 25% (482°F to 662°F)
Temperatures above 350°C (662°F) are not permitted.
11. RUD-Lifting points must not be used under chemical influences such as acids, alkaline solutions and vapours e.g. in pickling baths or hot dip galvanising plants. If this cannot avoided, please contact the manufacturer indicating the concentration, period of penetration and temperature of use.
12. The places where the lifting points are fixed should be marked with colour.
13. After fitting, an annual inspection or sooner if conditions dicate should be undertaken by a competent person examining the continued suitability. Also after damage and special occurrences.
Inspection criteria concerning paragraphs 2 and 13:
- Ensure correct bolt and nut size, quality and length.
- Ensure compatibility of bolt thread and tapped hole - control of the torque.
- The lifting point should be complete.
- The working load limit and manufacturers stamp should be clearly visible.
- Deformation of the component parts such as body, load ring and bolt.
- Mechanical damage, such as notches, particularly in high stress areas.
- Wear should be no more than 10% of cross sectional diameter.
- Evidence of corrosion.
- Evidence of cracks.
- Damage to the bolt, nut and/or thread.
- The body of the VLBG must be free to rotate.
Pricing
Unfortunately, this product has been discontinued and/or is no longer available. Please contact us for details on possible alternative products.
Contact Us About This ProductUnfortunately the RUD LBG Stainless Hoist ring is no longer available. Please see our range of stainless steel lifting points for a possible alternative.
Can rotate through 360 degree, automatically adjusting to the adjusted to the direction of the lift.
The RUD lifting ring LBG swivel hoisting rings can rotate by 360°, aligned to the direction of lift, the load ring can be tilted and will give 100% WLL in all load directions. The bolt supplied with the LBG is captivated so that it becomes a part of the lifting assembly and is 100% crack detected. The maximum lengths of the screws are adjusted in a way that a material thickness of about 8xM (with M16 and M20) and can be mounted by using a hexagon nut (ISO 7084/7090).
Lifting safety can supply special length bolts to our customers specification.
For technical information please see the Load Charts, Technical Specifications or User Instructions tabs above.
Proof Testing
There is no requirement to Proof Test RUD Products, either Bolt or Weldable after Installation if the user instructions for welding are carried out correctly. The welding should be carried out by a suitably qualified and competent welder/person.
The supporting structure, or the load, should be of adequate strength to take the stresses involved and this is the responsibility of the engineering designer or equivalent.
RUD Lifting and Lashing Products are Manufactured and conform to EN 1677. No further Proof Testing in the field is required. In fact it would be considered that the Product had been overloaded if a Load more than the recommended Working Load Limit had been applied.
RUD products should be regularly inspected in line with the requirements of LOLER and as per our user instructions at intervals decided by a competent person.
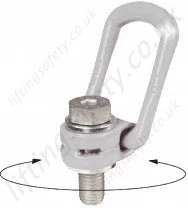
Load Charts - Metric and Imperial
Load Capacities - Metric Tonnes - Table 1
Method of lift | ![]() |
![]() |
![]() |
![]() |
![]() |
![]() |
![]() |
![]() |
|||
Number of legs | 1 | 1 | 2 | 2 | 2 | 2 | 2 | 3 and 4 | 3 and 4 | 3 and 4 | |
Angle of inclination <ß | 0° | 90° | 0° | 90° | 0-45° | 45-60° | unsymm. | 0-45° | 45-60° | unsymm. | |
Factor | 1 | 1 | 2 | 2 | 1,4 | 1 | 1 | 2,1 | 1,5 | 1 | |
Type Thread | WLL in metric tonnes, bolted and adjusted to the direction of pull | ||||||||||
LBG 1t | M16 | 1 t | 1 t | 2 t | 2 t | 1.4 t | 1 t | 1 t | 2.1 t | 1.5 t | 1 t |
LBG 2t | M20 | 2 t | 2 t | 4 t | 4 t | 2.8 t | 2 t | 2 t | 4.2 t | 3 t | 2 t |
Load Capacities - Imperial lbs - Table 2
Method of lift | ![]() |
![]() |
![]() |
![]() |
![]() |
![]() |
![]() |
![]() |
|||
Number of legs | 1 | 1 | 2 | 2 | 2 | 2 | 2 | 3 and 4 | 3 and 4 | 3 and 4 | |
Angle of inclination <ß | 0° | 90° | 0° | 90° | 0-45° | 45-60° | unsymm. | 0-45° | 45-60° | unsymm. | |
Factor | 1 | 1 | 2 | 2 | 1,4 | 1 | 1 | 2,1 | 1,5 | 1 | |
Type Thread | WLL in imperial lbs, bolted and adjusted to the direction of pull | ||||||||||
LBG 1t | M16 | 2200 lbs | 2200 lbs | 4400 lbs | 4400 lbs | 3086 lbs | 2200 lbs | 2200 lbs | 4630 lbs | 3307 lbs | 2200 lbs |
LBG 2t | M20 | 4400 lbs | 4400 lbs | 8800 lbs | 8800 lbs | 6172 lbs | 4400 lbs | 4400 lbs | 9260 lbs | 6614 lbs | 4400 lbs |
Technical Dimensions - Table 3
All dimensions are in millimetres (mm) unless otherwise stated.
|
|||||||||||||||||||||||||
Model | WLL (t) | Weight (kg) | A (mm) | B max. | C | D | E | F | G | H std. | H max. | J | K | L std. | L max. | M (mm) | N | SW | R | T | DB | Thread Pitch (mm) | torque | Standard | |
Metric Threads | |||||||||||||||||||||||||
LBG (3) M16 RS 1t | 1 | 1 | 50 | 85 | 50 | 45 | 43 | 16,5 | 38 | 25 | - | 95 | 45 | 63 | - | 16 | - | 24 | 46 | 88 | 40 | 2 | 100 Nm | 62086 INOX | |
LBG (3) M20 RS 2t | 2 | 1,1 | 50 | 85 | 50 | 46 | 42 | 16,5 | 38 | 27 | - | 95 | 45 | 65 | - | 20 | - | 30 | 46 | 88 | 40 | 2.5 | 200 Nm | 62813 INOX |
User Instructions
1. Reference should be made to German Standards accord. BGR 500 or other country specific statutory regulations and inspections are to be carried out by competent persons only.
2. Before installing and every use, visually inspect RUD lifting points, paying particular attention to any evidence of corrosion, wear and weld cracks and deformations. Please ensure compatibility of bolt thread and tapped hole.
3. The material construction to which the lifting point will be attached should be of adequate strength to withstand forces during lifting without deformation. The German testing authority BG, recommends the following minimum for bolt lengths:
1 x M in steel (minimum quality S235JR [1.0037])
1,25 x M in cast iron (for example GG 25)
2 x M in aluminium alloys
2,5 x M in aluminium-magnesium alloys
( M = diameter of RUD lifting point bolt, for ex. M 20 )
When lifting light metals, nonferrous heavy metals and gray cast iron the thread has to be chosen in such a way that the working load limit of the thread corresponds to the requirements of the respective base material.
RUD lifting points are delivered with a 100 % crack tested bolt (length up to lmax please see chart 2). When using your own bolts, the bolts have to be 100% crack tested. The min quality of the hexagon bolt had to be 10.9 accord. EN 24014 (DIN 931) with the nominal diameter. For replacement the bolt can be easily hammered out (M8 - M30). The type VLBG 7t M36 is only delivered with a special bolt, therefore it is not possible to use a EN/DIN-bolt.
RUD supplies the Vario length complete with a washer and crack-detected nut corresponding to DIN 980.
4. The lifting points must be positioned on the load in such a way that movement is avoided during lifting.
a.) For single leg lifts, the lifting point should be vertically above the centre of gravity of the load.
b.) For two leg lifts, the lifting points must be equidistant to/or above the centre of gravity of the load.
c.) For three and four leg lifts, the lifting points should be arranged symmetrically around the centre of gravity in the same plane if possible.
5. Load Symmetry:
The working load limit of individual RUD lifting points are calculated using the following formula and are based on symmetrical loading:
WLL =
|
G n x cos ß |
WLL = Working Load Limit G = Load Weight (kg) n = Number of load bearing legs ß = Angle of inclination of the chain to the vertical |
The calculation of load bearing legs is as follows:
No. Legs | Symmectrical | Asymmetrical |
Two Leg | 2 | 1 |
Three / Four Leg | 3 | 2 |
(See Table 1 and 2)
6. A Plane bolting surface (ØDB) must be guaranteed. The holes must be drilled with a sufficient depth in order to guarantee compatibility with the supporting surface.
7. The LBG has to be adjustable through 360° when fitted.
For single use just tighten with spanner. For long term application the VLBG should be tightened with torque according to table 2 (+/- 10%).
In case of turning movements (continuous operation) the recommended torques have to be checked regularly (For turning movements we recommend to use the RUD lifting point PowerPoint, WBG-V or WBG).
Adjust to the direction of pull, before attaching to the lifting means. The load ring should be free moving and should not be touching edges.
8. All fittings connected to the VLBG should be free moving. When connecting and disconnecting the lifting means (sling chain) pinches and impacts should be avoided. Damage of the lifting means caused by sharp edges should be avoided as well.
9. To prevent unintended dismounting through shock loading, rotation or vibration thread locking fluid such as Loctite (depending on the application, please pay attention to the manufacturer's instruction) could be used to secure the bolt, or use form-closed devices.
10. Effects of temperature:
Due to the DIN/EN bolts that are used with the VLBG the working load limit should be reduced accordingly:
-40° to 100°C = no reduction (-40°F to 212°F)
100° to 200°C = minus 15% (212°F to 392°F)
200° to 250°C = minus 20% (392°F to 482°F)
250° to 350°C = minus 25% (482°F to 662°F)
Temperatures above 350°C (662°F) are not permitted.
11. RUD-Lifting points must not be used under chemical influences such as acids, alkaline solutions and vapours e.g. in pickling baths or hot dip galvanising plants. If this cannot avoided, please contact the manufacturer indicating the concentration, period of penetration and temperature of use.
12. The places where the lifting points are fixed should be marked with colour.
13. After fitting, an annual inspection or sooner if conditions dicate should be undertaken by a competent person examining the continued suitability. Also after damage and special occurrences.
Inspection criteria concerning paragraphs 2 and 13:
- Ensure correct bolt and nut size, quality and length.
- Ensure compatibility of bolt thread and tapped hole - control of the torque.
- The lifting point should be complete.
- The working load limit and manufacturers stamp should be clearly visible.
- Deformation of the component parts such as body, load ring and bolt.
- Mechanical damage, such as notches, particularly in high stress areas.
- Wear should be no more than 10% of cross sectional diameter.
- Evidence of corrosion.
- Evidence of cracks.
- Damage to the bolt, nut and/or thread.
- The body of the VLBG must be free to rotate.
Contact Us About This Product
If you wish to receive a quote for this product, please use the tab above, this form is for general enquiries regarding this product only.
You can also Request a Quote using the Quote tab above!
You can easily add more than one item to the Quote Request. This is highly recommended as we will be able to suit your needs much more efficiently.
Share this page!
